Case Studies / Fuji Xerox
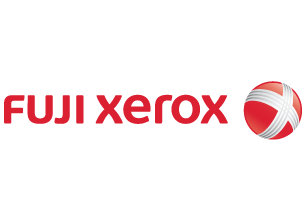
Reduce the Lead Time to Visualisation
Real-Time Monitoring Improves the Production Process
Fuji Xerox’s manufacturing business is responsible for producing printer parts and consumables such as toner.
The company has long embraced the power of data to improve the manufacturing process. However, prior to the introduction of MotionBoard, much of the data generated by the factory for its quality control processes was collected through handwritten reports. This information was then re-entered into Excel in a time consuming and error prone process, taking up to 80 minutes.
While the Excel data was being collated on a weekly basis by the Quality Management department to generate an aggregated monthly management report, these reports were not an effective tool for reducing defects, as too much time passed between collecting the data and analysing the results: it often took 2-3 days’ lead time to collate the data, visualise the results, estimate the cause of failure and implement a remedy. The organisation needed a solution that could both reduce input time and quickly identify the cause of failure, rather than allowing the issue to continue causing defects on the production line.
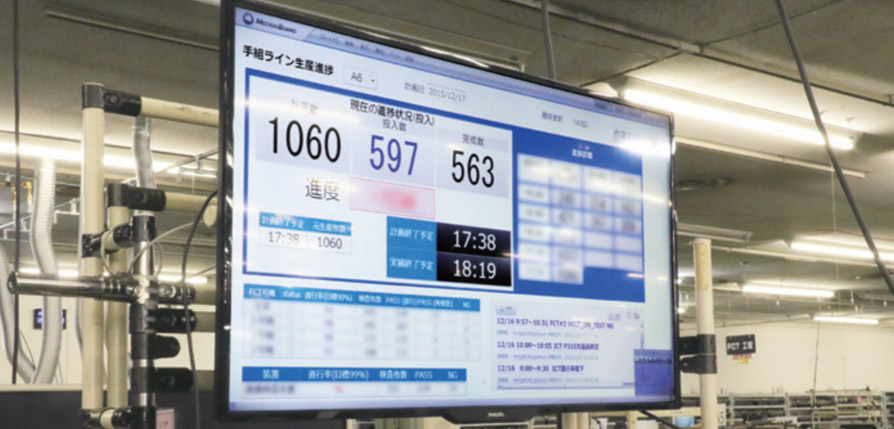
To remedy this, Fuji Xerox introduced MotionBoard, along with iPads on the factory floor for direct data input. The initial trial in December 2014 focused on the production line for copier parts, and quickly convinced senior management of its effectiveness by helping to find and eliminate defects at source. Following the success of the trial, MotionBoard was quickly approved for use across the factory.
While the switch to iPads in the field was initially met with some resistance, employees quickly realised the new process was much easier than before. Most of the data input could be done with one touch, or by scanning a barcode. What had once taken up to 80 minutes of labourious data entry in Excel was now reduced to effectively 0 minutes.
Before
Hand written daily reports were manually entered into Excel, taking up to 80 minutes a day.
Improving productivity and reducing defects was not easy, due to the significant lead time between collecting data and making it available for analysis through the monthly reports.
After
Data input time has dramatically reduced, with direct input using iPads replacing a highly manual process.
The end result has been a reduction in overtime hours, and a steady decrease in the number of defects: issues can now be visualised and resolved in near real time.